Understanding the **Injection Nozzle in Diesel Engines**
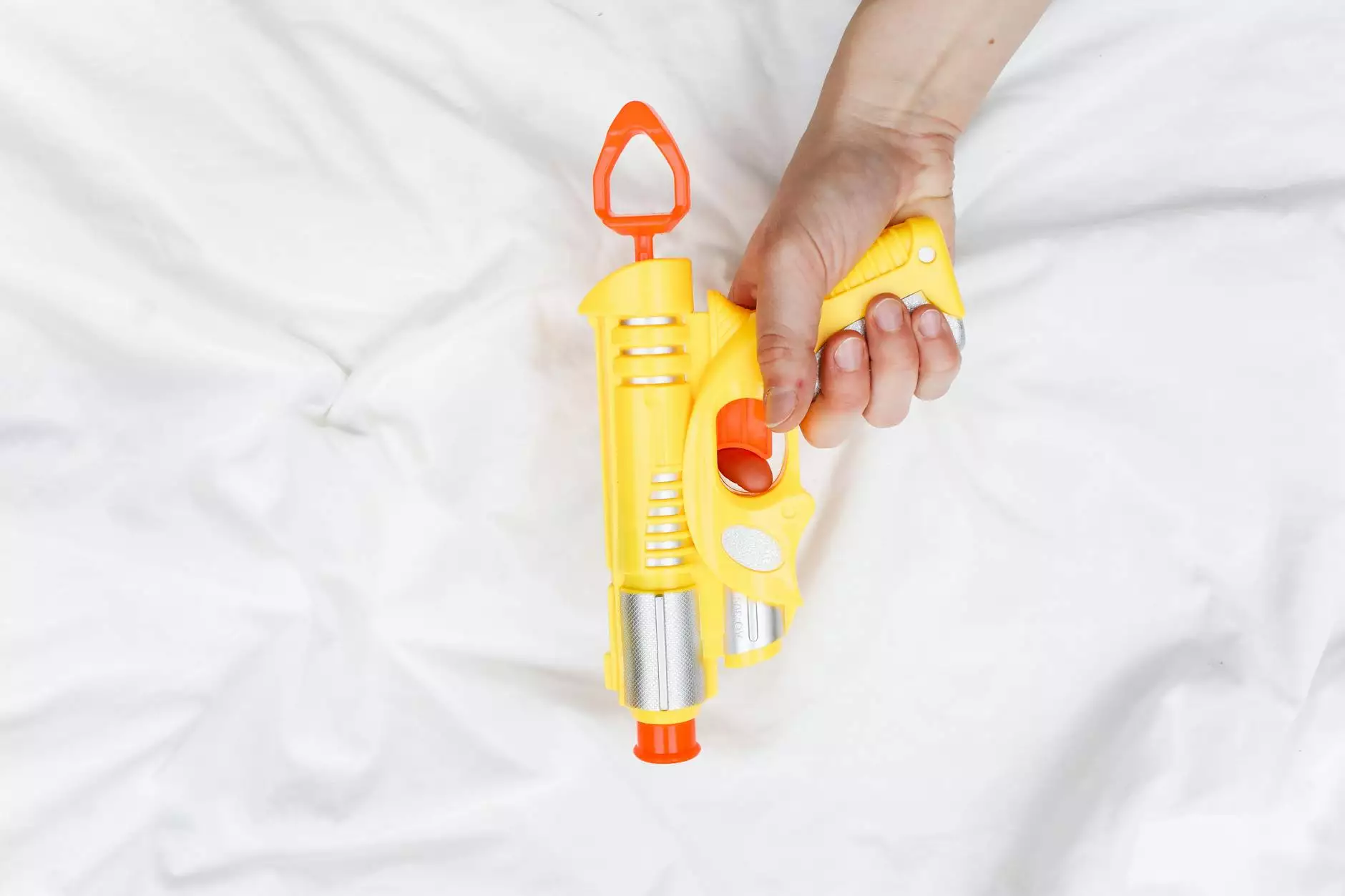
The injection nozzle in diesel engines is a pivotal component that directly influences the engine's performance, efficiency, and emissions. It plays a significant role in the diesel combustion process and is integral to the overall functionality of diesel engines. In this article, we will delve into the various aspects of injection nozzles, including their design, operation, maintenance, and the latest advancements in technology.
What is an Injection Nozzle?
An injection nozzle is a precision device that atomizes and injects diesel fuel into the combustion chamber of a diesel engine. This component plays a crucial role in ensuring an efficient combustion process, generating the necessary power to drive the engine. The nozzle's design allows for the fine distribution of fuel, promoting better mixing with air, which is essential for optimal combustion.
Functionality of the Injection Nozzle in Diesel Engines
The primary function of the injection nozzle in diesel engines involves several critical processes that contribute to overall engine efficiency. Below are the main functions:
- Atomization: The injection nozzle atomizes the diesel fuel, turning it into a mist that can mix with the compressed air in the combustion chamber, facilitating an efficient combustion process.
- Fuel Delivery: The nozzle delivers the correct amount of fuel at the precise moment in the combustion cycle, ensuring maximum power output and minimal emissions.
- Pressure Management: It helps manage fuel pressure, ensuring optimal performance while protecting the engine components from potential damage caused by excessive pressure.
- Emissions Control: By optimizing the fuel-air mixture, the nozzle contributes to lower emissions and helps meet environmental standards.
Types of Injection Nozzles
There are several types of injection nozzles employed in diesel engines, each serving specific needs and applications:
1. Mechanical Injection Nozzles
These nozzles operate purely on mechanical principles, relying on the engine's injection pump to deliver fuel at the right pressure. They are commonly found in older diesel engines due to their simplicity and durability.
2. Electronic Injection Nozzles
Modern diesel engines often use electronic fuel injection systems, where nozzles are controlled by electronic actuation. This allows for precise timing and fuel delivery, enhancing fuel efficiency and performance.
3. Common Rail Injection Nozzles
Common rail systems store fuel at high pressure, and multiple nozzles can be activated in quick succession. This setup allows for multiple injections per cycle, improving combustion and reducing emissions.
The Design of the Injection Nozzle
The design of an injection nozzle significantly impacts its performance. Here are key design features that enhance functionality:
- Spray Pattern: The angle and shape of the spray pattern are critical for ensuring optimal fuel dispersion in the combustion chamber.
- Nozzle Tip Configuration: The nozzle tip design influences fuel atomization. Advanced designs improve distribution and combustion efficiency.
- Material Selection: High-performance materials resistant to heat and wear enhance the nozzle's lifespan and reliability.
Importance of Proper Maintenance
Maintaining the injection nozzle in diesel engines is essential for ensuring longevity and optimal performance. Here are some maintenance tips:
1. Regular Inspection
Periodic checks can help identify signs of wear or clogging. Look for symptoms such as rough idling, decreased fuel efficiency, or increased emissions.
2. Cleaning
Regular cleaning of the injectors can improve performance. Specialized cleaning agents can help dissolve deposits and enhance fuel flow.
3. Replacement
If inspection reveals significant wear or damage, replacing the nozzle is necessary to restore engine performance and efficiency.
Technological Advancements in Injection Nozzle Design
Recent advancements have significantly enhanced the functionality of injection nozzles, leading to better performance and efficiency:
1. Multi-Hole Nozzle Technology
Multi-hole nozzles allow for finer fuel atomization and better spray patterns, which leads to improved combustion efficiency and reduced emissions.
2. Piezoelectric Actuation
Piezoinjectors provide greater control over fuel delivery, allowing for rapid adjustments in timing and quantity, essential for modern diesel engines with strict emission standards.
3. Advanced Coatings
New coatings that resist corrosion and wear can extend the life of injectors and maintain their performance over longer periods.
Challenges and Solutions in Injection Nozzle Performance
Though the injection nozzle in diesel engines is an essential component, it faces several challenges:
1. Fuel Quality
Poor-quality diesel can lead to injector clogging and wear. Ensuring the use of high-quality fuel is fundamental for maintaining performance.
2. Temperature Variations
Extreme temperatures can affect fuel viscosity and injection timing. Maintaining optimal engine temperatures is crucial for nozzle performance.
3. Maintenance and Servicing
Neglecting regular maintenance can lead to significant performance issues. Operators should adhere to recommended service intervals.
Conclusion
Understanding the injection nozzle in diesel engines is critical for anyone looking to improve engine performance, efficiency, and environmental compliance. By focusing on the design, functionality, maintenance, and the latest technological advancements, operators and mechanics can ensure that their diesel engines run smoothly and efficiently. The importance of high-quality diesel engine parts and reliable spare parts suppliers cannot be overstated, as they are integral to keeping these systems operating at peak performance. At client-diesel.com, we offer a wide range of high-quality diesel engine components, ensuring your engines perform optimally for years to come.