Die Casting Mold Company: Your Partner in Precision and Quality
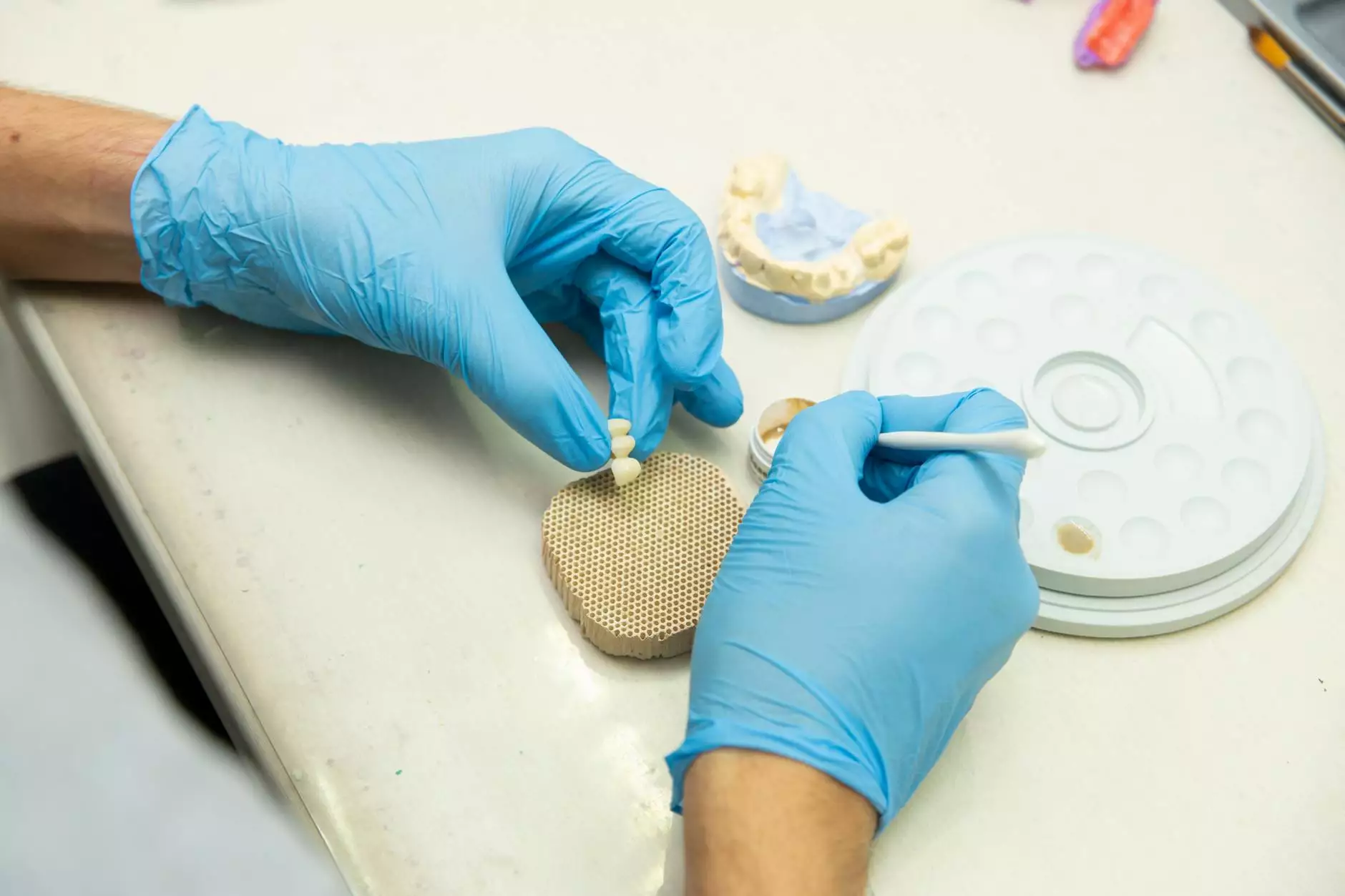
Understanding Die Casting in Today's Manufacturing Landscape
In an era where precision and efficiency are paramount, the role of a die casting mold company cannot be overstated. Die casting is a manufacturing process that involves forcing molten metal into a mold to create intricate parts with superior finish and accuracy. This method is extensively utilized in various industries, including automotive, electronics, and consumer goods. The growing demand for lightweight yet durable components has catalyzed advancements in die casting technology, making it an essential component of modern manufacturing.
The Importance of Quality in Die Casting Mold Manufacturing
Quality is the cornerstone of successful die casting operations. A reliable die casting mold company prioritizes the creation of molds that meet stringent industry standards. Here’s why quality is crucial:
- Durability: High-quality molds withstand the rigors of production, reducing the risk of failure and increasing lifespan.
- Precision: Accurate molds ensure that the components produced fit perfectly, which is especially important in sectors like aerospace and automotive.
- Cost-Effectiveness: Although initial investments in quality molds may be higher, they lead to reduced maintenance and higher productivity over time.
Choosing the Right Die Casting Mold Company
Selecting a die casting mold company can be a daunting task. Here are some key considerations to guide your choice:
- Experience and Expertise: Look for a company with a proven track record in die casting mold manufacturing.
- Range of Services: A versatile company offers design, prototyping, and production services.
- Technology and Innovation: Top-tier companies leverage the latest technologies, such as 3D printing and CAD software, to enhance mold design and precision.
- Customer Support: Excellent customer service ensures that clients remain informed throughout the process, from design to delivery.
The Die Casting Process Explained
The die casting process is intricate yet highly efficient. Here’s a breakdown of the typical stages involved:
1. Mold Design
The process begins with designing the mold, which involves careful consideration of the product specifications and requirements.
2. Mold Construction
Once the design is finalized, skilled technicians manufacture the mold using high-quality materials, typically steel or aluminum, known for their strength and durability.
3. Melting the Metal
In this stage, the metal (commonly aluminum, zinc, or magnesium) is heated to its melting point in a furnace.
4. Injection
The molten metal is then injected into the mold under high pressure. This ensures that the metal fills all cavities, resulting in a detailed and accurate part.
5. Cooling and Ejection
After sufficient cooling, the mold is opened, and the die cast part is ejected. This part is then inspected for quality assurance.
Applications of Die Casting in Various Industries
Die casting is a versatile technique used across numerous industries:
- Automotive Industry: Used for making engine blocks, transmission cases, and multiple other components that require strength and lightweight characteristics.
- Consumer Electronics: Frequently used in the production of smartphones, laptops, and other electronic enclosures.
- Aerospace: Critical for components requiring high durability and low weight, improving fuel efficiency.
- Medical Devices: In the fabrication of intricate parts that must meet stringent regulatory standards.
Innovations in Die Casting Technologies
The die casting industry is experiencing rapid technological advancements. Some noteworthy trends include:
1. Cold Chamber Die Casting
This technique is particularly suitable for metals with high melting points. It separates the furnace from the die, enhancing efficiency.
2. 3D Printing and Rapid Prototyping
3D printing technology enables companies to create prototypes quickly, allowing for faster iterations and more efficient design processes.
3. Smart Manufacturing
Integrating IoT technology into die casting operations leads to improved monitoring, predictive maintenance, and efficiency.
Environmental Considerations in Die Casting
Sustainability is a growing concern in all manufacturing processes, and die casting is no exception. Companies are increasingly adopting eco-friendly practices to minimize their environmental footprint. Some effective strategies include:
- Recycling Metal: Utilizing scrap metal reduces waste and the need for raw materials, promoting a circular economy.
- Energy Efficiency: Implementing energy-efficient machinery and processes to lower energy consumption.
- Pollution Control: Adopting technologies and practices to reduce emissions and ensure cleaner operations.
Conclusion: The Future of Die Casting
The future of the die casting mold company lies in its ability to adapt to market demands, innovate, and prioritize quality. As industries continue to evolve, the die casting process will play an integral role in the production of high-quality parts that meet the stringent requirements of modern applications. By partnering with a reputable die casting mold company, businesses can ensure they are equipped to handle the challenges of tomorrow's manufacturing needs.
For more information about our services or to receive a personalized quote, visit us at deepmould.net.